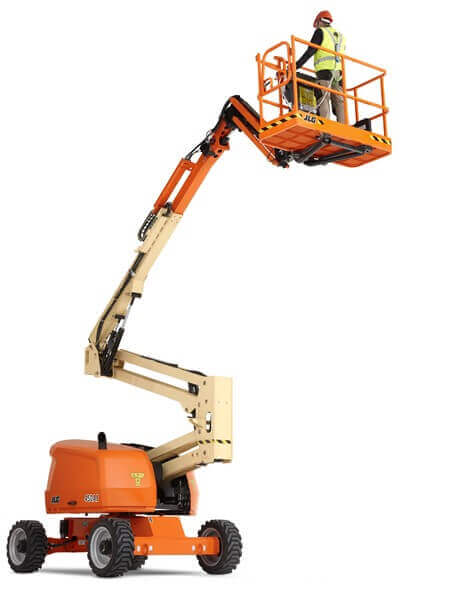
404
Oops… you can’t reach us here.
The link you followed may have been broken, or the page may have been removed.
Let us give you a lift to our home page or any of our other useful pages:
Rental
Sales
Training
Parts
Maintenance
Our locations
Careers
Can’t find what you’re looking for? Please contact us on +31 (0)88 618 18 18 or info@riwal.com.